Mastering Equipment Parts: A Comprehensive Guide to Optimal Performance and Longevity
In today's industrial landscape, the efficient operation of machinery is heavily reliant on the quality and longevity of its equipment parts. According to a report by the National Institute of Standards and Technology, improper maintenance and subpar part selection can lead to equipment failure rates as high as 30%, significantly impacting productivity and operational costs. With industries facing increasing pressures to enhance performance while minimizing downtime, understanding the intricacies of equipment parts has never been more critical.
Moreover, a study by the Machinery Manufacturers Association reveals that around 70% of maintenance budgets are spent on reactive repairs rather than proactive optimization strategies. This statistic underscores the importance of mastering the various aspects of equipment parts not only to extend their life cycle but also to optimize overall machinery performance. This comprehensive guide aims to delve into the best practices surrounding equipment parts, highlighting key insights and methodologies that can empower operators and maintenance personnel to achieve peak efficiency and durability in their operations.
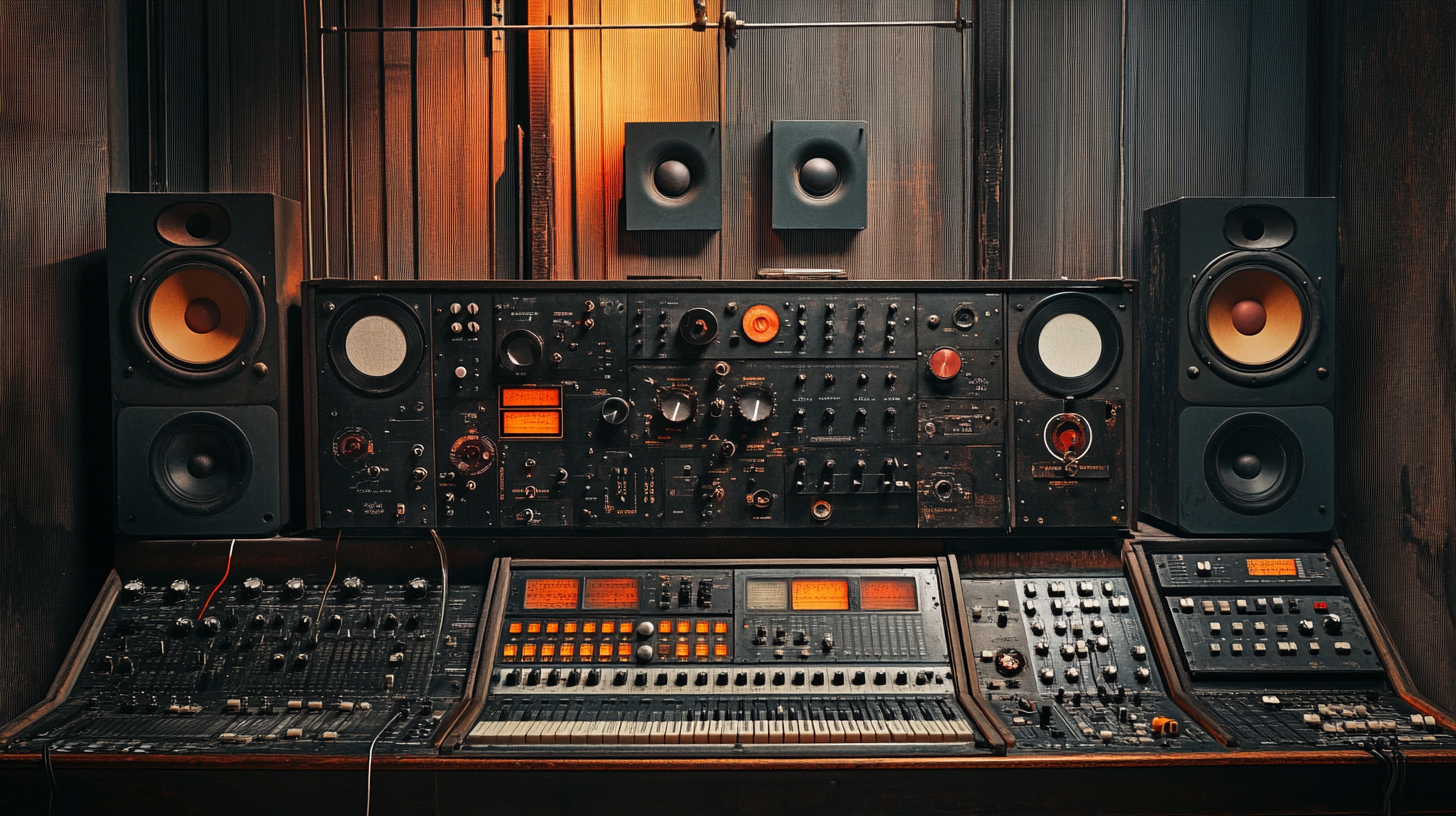
Understanding Equipment Parts: Key Components for Enhanced Performance
In today’s fast-paced technological landscape, understanding the key components of equipment parts is essential for enhancing performance across various industries. For instance, the introduction of the new Porsche 911 Carrera GTS, which features a super-lightweight performance hybrid system, exemplifies how advancements in equipment components can lead to significantly improved performance metrics. The integration of hybrid technology signifies a shift towards optimizing every part to elevate overall vehicle efficiency and responsiveness, a concept that applies across many sectors. Similarly, the aerospace and defense industry is poised for operational breakthroughs as it embraces a wide range of innovative technologies. According to the 2025 Aerospace and Defense Industry Outlook, predictive modeling and advanced analytics will play pivotal roles in transforming operational functions. This paradigm shift underscores the importance of understanding the intricate parts that constitute a system, as they can directly affect performance, risk management, and operational longevity. Furthermore, in the realm of healthcare technology, machine learning is being leveraged to enhance predictive capabilities in identifying risk factors for strokes. Studies indicate that predictive modeling, fueled by data from equipment and patient monitoring systems, is becoming a game-changer in proactive healthcare. By analyzing the performance of each component within these systems, we can achieve remarkable advancements in patient outcomes and healthcare efficiency. Understanding the intricacies of equipment parts, therefore, is not just a matter of maintenance but a cornerstone of innovation and improved performance across myriad fields.
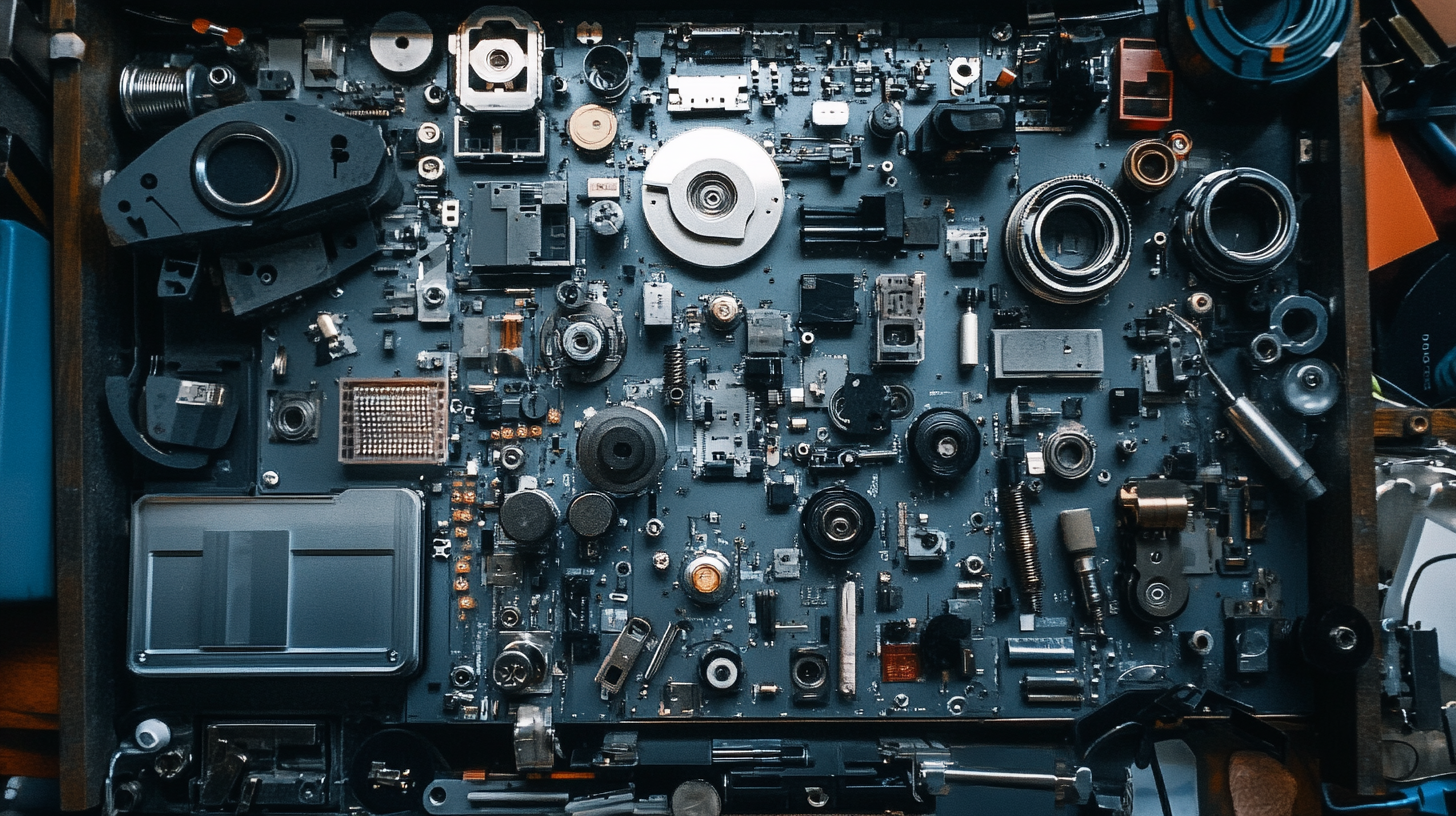
The Role of Regular Maintenance: Data-Driven Strategies for Longevity
Regular maintenance is crucial for optimizing equipment performance and ensuring its longevity. By employing data-driven strategies, organizations can transition from reactive to proactive maintenance practices, minimizing downtime and reducing operational costs. For instance, in industries like water utilities, artificial intelligence can predict potential failures in infrastructure, thus preventing costly repairs and water loss. This application of data analytics not only enhances reliability but also leads to substantial financial savings.
In the realm of industrial equipment, predictive maintenance has emerged as a powerful approach. By leveraging real-time data and machine learning algorithms, businesses can forecast maintenance needs before failures occur. This not only extends the lifespan of machinery but also boosts overall productivity. Additionally, industries are increasingly adopting automated maintenance management systems, which help streamline operations and foster a culture of continuous improvement. Such strategies not only ensure optimal performance but also align with sustainability goals by reducing waste and promoting resource efficiency.
Embracing these data-driven maintenance strategies is essential for organizations aiming to enhance equipment reliability while also achieving long-term strategic sustainability objectives. By focusing on regular maintenance and utilizing intelligent data analysis, companies can unlock the full potential of their equipment, leading to improved performance and significant cost savings.
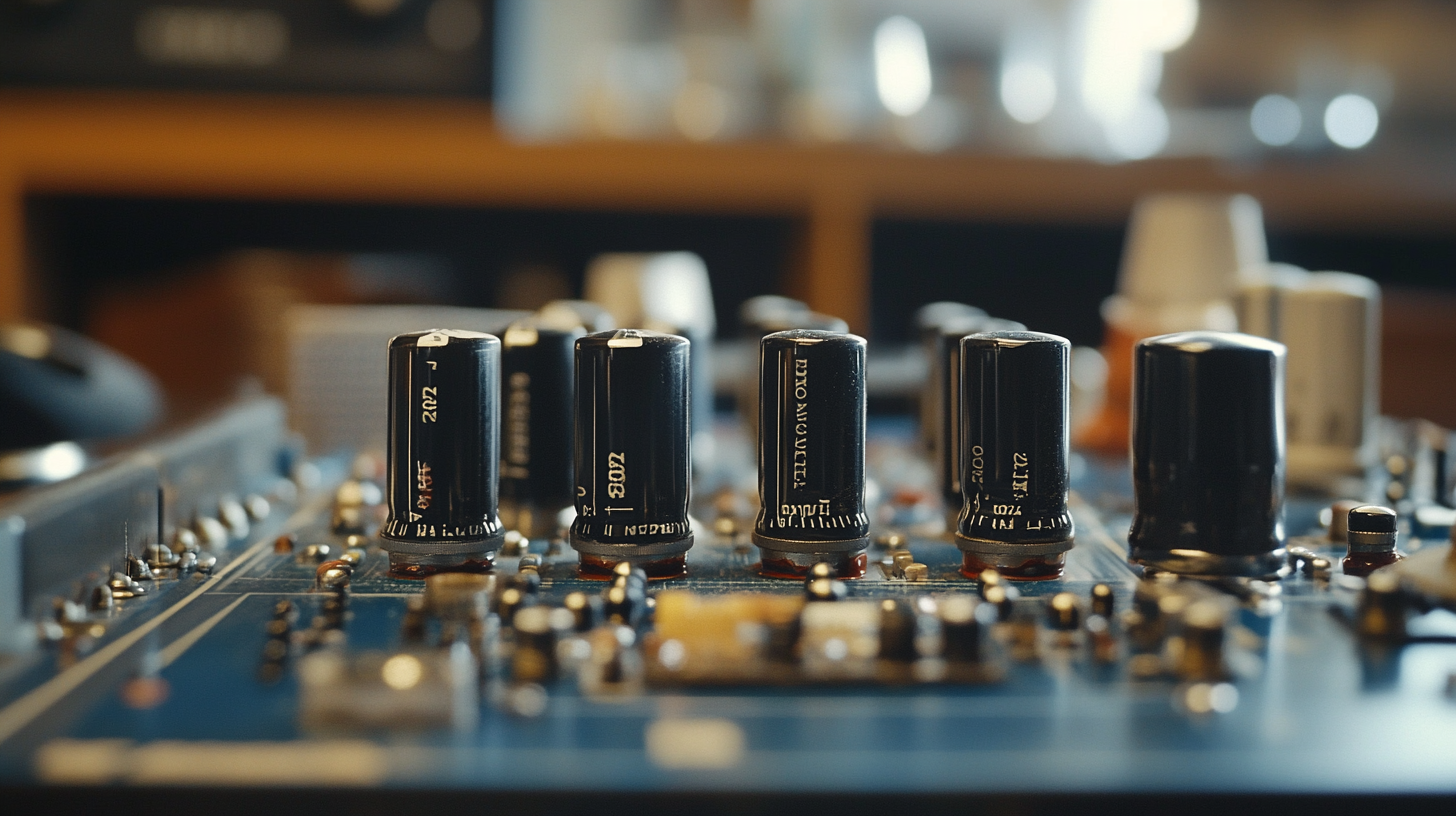
Common Equipment Failures: Statistics and Prevention Techniques
Common equipment failures can be costly, both in terms of direct repair expenses and the operational downtime they cause. A report by the U.S. Department of Energy indicates that unplanned outages can lead to lost productivity, costing organizations upwards of $1 million per hour in some sectors. In particular, industries such as manufacturing and energy face heightened risks due to the complexity of their machinery. For instance, the National Institute of Standards and Technology reports that nearly 20% of manufacturing equipment fails each year, primarily due to improper maintenance.
Preventive maintenance strategies are essential in minimizing these risks and ensuring optimal equipment performance. A study by the Reliabilityweb.com reveals that organizations implementing predictive maintenance can reduce equipment failure rates by 30-50%. Techniques such as vibration analysis and thermal imaging are invaluable for identifying potential issues before they escalate into major failures. Moreover, utilizing a robust maintenance management system helps track equipment performance metrics and schedules timely interventions, thus fostering a culture of proactive care.
Training staff to conduct regular inspections and understanding common failure modes can empower teams to identify early warning signs. According to a survey by the Maintenance Reliability Conference, over 70% of organizations that prioritize staff training and development report enhanced equipment reliability and longevity. By fostering a culture of awareness and maintenance diligence, businesses can significantly reduce the likelihood of failures, ensuring that equipment continues to operate at peak performance levels.
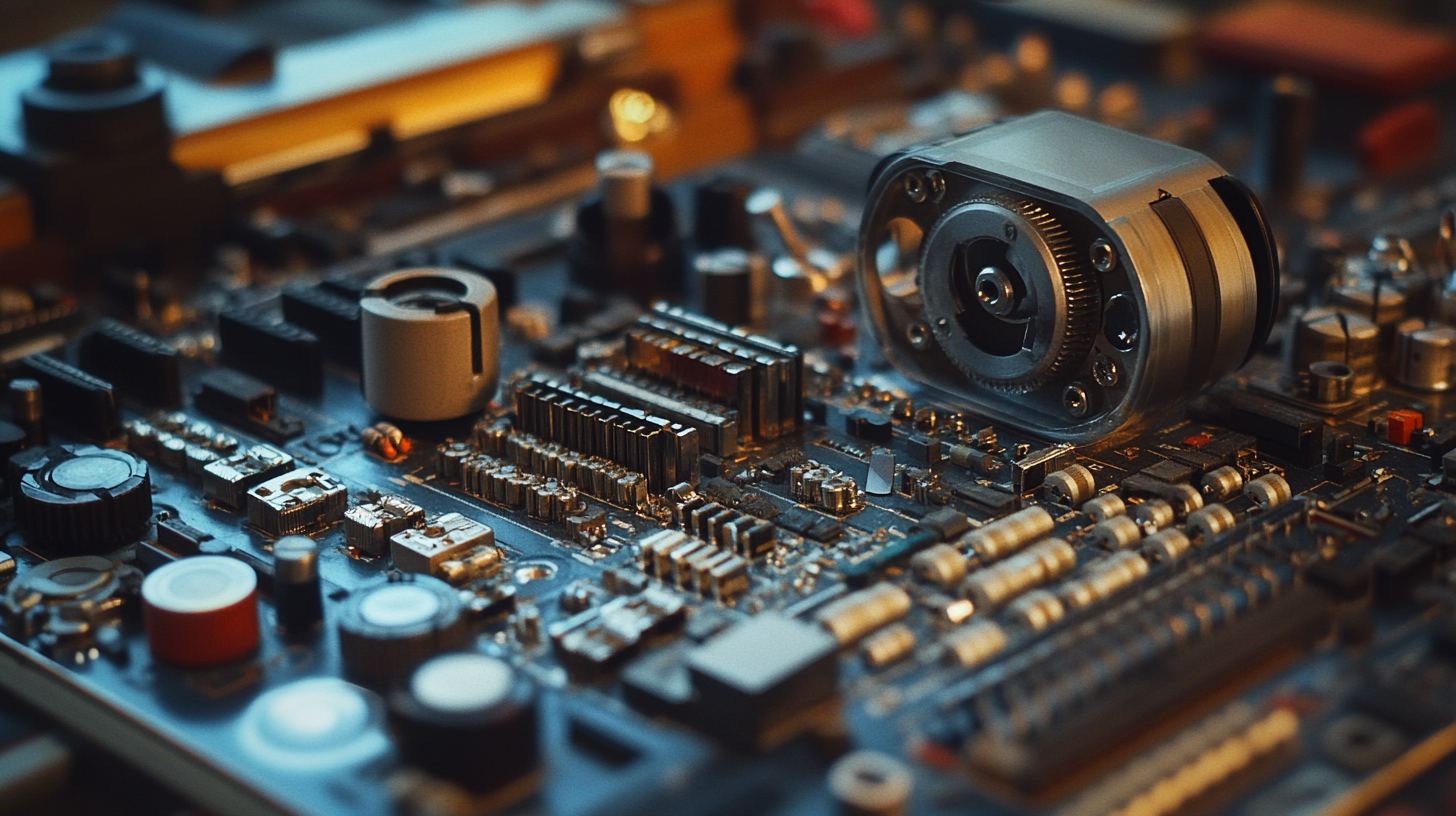
Material Selection Impact: How Quality Influences Performance and Durability
When it comes to equipment parts, the choice of materials is pivotal not only for performance but also for durability. High-quality materials can significantly enhance the function of machinery, influencing not just how well a piece operates but also how long it lasts. For instance, metals like stainless steel and titanium are often favored in demanding applications due to their resistance to corrosion and wear. Choosing the right materials can lead to fewer breakdowns and lower maintenance costs, ultimately translating into better productivity.
On the other hand, opting for subpar materials can compromise not only the equipment's effectiveness but also safety. Poor-quality components may fail prematurely, leading to costly repairs and potential hazards. It’s critical to assess the environmental conditions and operational demands when selecting materials. For example, in high-temperature settings, using specialized alloys can prevent deformation and extend life cycles. Therefore, understanding the influence of material selection on performance is essential for anyone looking to optimize their equipment investment.
Moreover, sustainability is becoming an increasingly important factor in material selection. Manufacturers are now looking towards eco-friendly materials that not only provide durability but also reduce the environmental impact. Advanced composite materials, for instance, offer an excellent blend of lightweight properties and strength. This focus on sustainability doesn't just benefit the planet; it also appeals to consumers and companies that prioritize corporate social responsibility. Thus, the implications of material selection extend beyond immediate performance and longevity, positioning businesses for future success in a changing market landscape.
Technological Advancements: Innovative Solutions for Optimal Equipment Efficiency
In today's rapidly evolving industrial landscape, technological advancements play a crucial role in enhancing equipment efficiency. With the integration of smart technologies and IoT, equipment can now communicate data in real-time, enabling predictive maintenance and minimizing downtime. According to a report by McKinsey, companies that implement IoT solutions in their operations can achieve up to a 30% reduction in equipment maintenance costs and a 10% increase in overall operational efficiency.
Furthermore, innovative solutions such as robotic process automation (RPA) are reshaping traditional workflows. According to a survey conducted by Deloitte, 53% of organizations have adopted RPA, resulting in an impressive 30% increase in productivity and significant cost savings. This technology not only streamlines processes but also allows workers to focus on more strategic tasks, further enhancing the overall performance of equipment.
Investing in advanced analytics tools is another key area influencing optimal equipment performance. As per a report from Gartner, predictive analytics can improve equipment lifespan by up to 20% when utilized effectively. By analyzing historical data and identifying patterns, organizations can foresee potential failures before they occur, thus ensuring that equipment operates at peak efficiency and contributes to overall productivity.
In conclusion, leveraging these innovative solutions and technological advancements is essential for achieving optimal equipment efficiency and longevity, empowering organizations to thrive in a competitive marketplace.